Understanding Die Casting: Revolutionizing Metal Fabrication
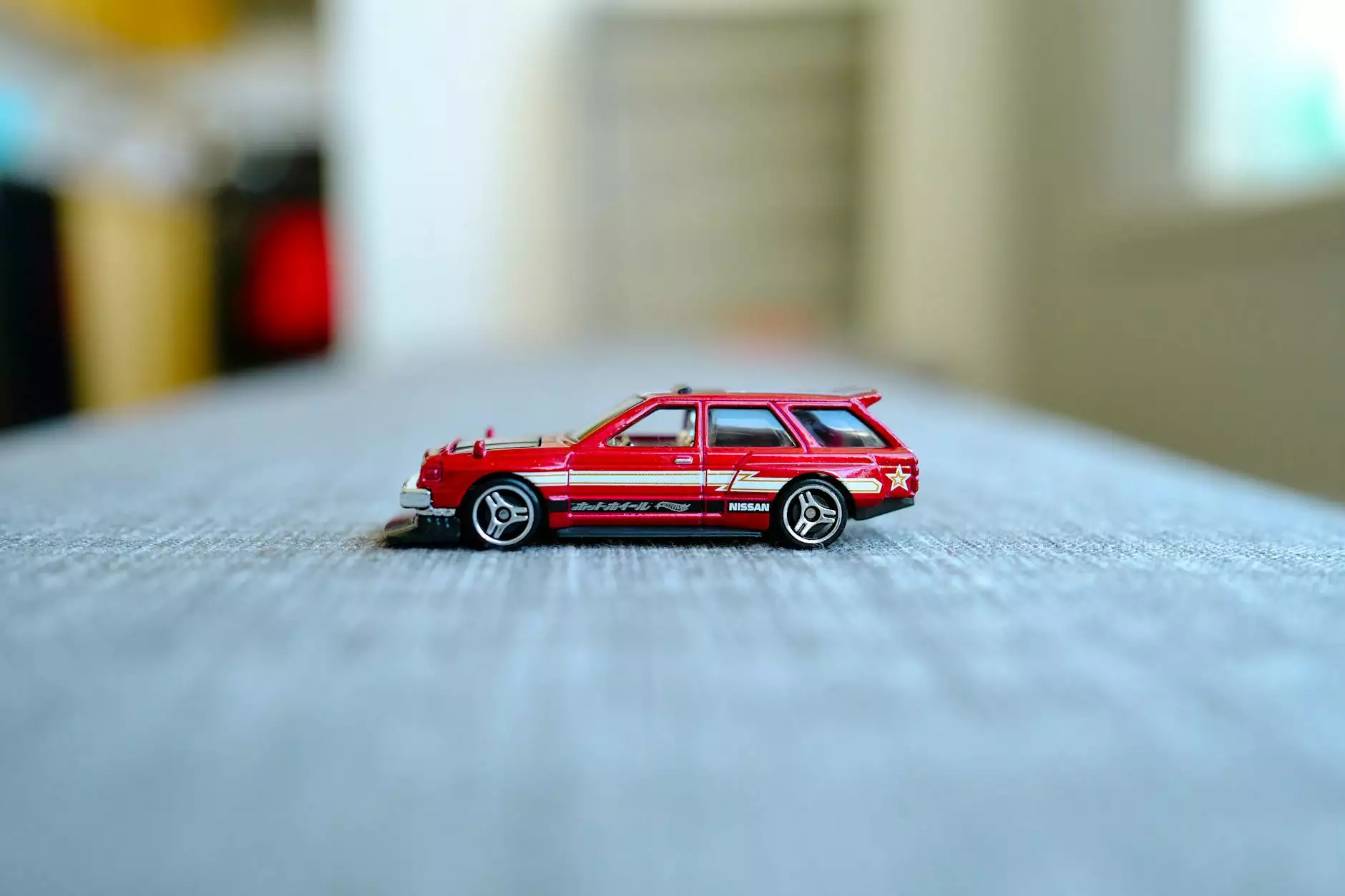
What is Die Casting?
Die casting is a highly efficient metal fabrication process that involves injecting molten metal into a mold under high pressure. This remarkable technique is widely used in the manufacturing of various metal components that require a high degree of precision and intricate detail. The metals typically used in die casting include aluminum, zinc, magnesium, copper, and lead.
The History of Die Casting
The origins of die casting can be traced back to the late 19th century. The first patent for a die casting machine was filed in 1838, revolutionizing the production of metal components. However, it was not until the 1920s that the process was refined and adopted for large-scale manufacturing. Today, die casting is integral to various industries, including automotive, aerospace, electronics, and consumer products.
How Die Casting Works
The die casting process can be broken down into several key steps:
- Mold Preparation: The die or mold is meticulously designed and manufactured to ensure accurate dimensions. The mold is typically composed of two halves that are precisely engineered to fit together.
- Melting the Metal: The selected metal is heated in a furnace until it reaches a molten state. The temperature varies depending on the type of metal used.
- Injection: Once the metal is molten, it is injected into the mold cavity under high pressure. This pressure forces the metal to fill every intricate detail of the mold, ensuring a perfect fit.
- Cooling: After the metal has been injected, it is allowed to cool and solidify within the mold. This step is crucial for maintaining dimensional accuracy.
- Demolding: Once the metal has cooled and solidified, the mold is opened and the finished component is ejected.
Benefits of Die Casting
Die casting offers numerous advantages that make it a preferred choice among manufacturers:
- High Precision: The process allows for the production of highly detailed components with tight tolerances, reducing the need for extensive machining.
- Efficiency: Die casting enables rapid production rates, making it ideal for high-volume manufacturing.
- Material Utilization: This process minimizes waste since the molten metal is precisely injected into the mold, leading to better yield.
- Diverse Materials: A wide range of metals can be used, providing manufacturers with flexibility in material selection based on performance needs.
- Excellent Surface Finish: Components produced through die casting often require minimal finishing, saving time and resources in the manufacturing process.
- Reduced Labor Costs: Automation possibilities in die casting lead to lower labor involvement, enhancing cost-effectiveness in large production runs.
Applications of Die Casting
Die casting is utilized across a broad spectrum of industries due to its versatility. Some notable applications include:
Automotive Industry
The automotive industry is one of the largest consumers of die-cast components. Parts such as engine blocks, transmission cases, and housings are commonly produced using this technique due to their durability and precision.
Aerospace Sector
In the aerospace sector, die casting is used for the production of lightweight and high-strength components, which are crucial for performance and fuel efficiency. Components such as landing gears and structural elements are often manufactured using die casting methods.
Electronics
With the rise of consumer electronics, die casting plays a significant role in producing parts like housings and brackets for various electronic devices. Its ability to create intricate designs makes it perfect for today's high-tech gadgets.
Consumer Products
Everyday products such as tools, appliances, and decorative items also benefit from die casting. The manufacturing process allows for intricate designs that enhance both functionality and aesthetic appeal.
Types of Die Casting Processes
There are two primary types of die casting processes: hot-chamber die casting and cold-chamber die casting. Understanding these methods can help in selecting the right approach for your manufacturing needs.
Hot-Chamber Die Casting
In hot-chamber die casting, the metal is melted in a furnace that is directly connected to the injection system. This method is ideal for metals with low melting points, such as zinc and magnesium. The advantages include:
- Faster production rates: The process allows for quicker injection cycles.
- Lower Die Wear: Since the metal does not cool significantly before injection, it reduces wear on the die.
Cold-Chamber Die Casting
Cold-chamber die casting involves pouring the molten metal into a chamber where it is then injected into the mold. This method is suitable for metals with higher melting points, like aluminum and copper. Some benefits include:
- Flexibility: It allows for a wider range of metals to be utilized.
- Higher Quality Castings: The process tends to produce higher quality castings with less oxidation.
The Die Casting Industry: Key Players and Competitors
The die casting industry is comprised of numerous manufacturers, suppliers, and service providers. Major players include:
- Alcoa Corporation: A leader in aluminum production and die casting.
- Castrol: Known for producing high-quality die casting lubricants.
- RICO Manufacturing: Specializes in custom die casting solutions.
- Dynacast: A global leader specializing in precision die casting.
Challenges in Die Casting
Despite its many advantages, the die casting industry faces several challenges:
- High Initial Setup Costs: The investment in quality molds and machinery can be significant, making it costly for smaller manufacturers to enter the market.
- Environmental Concerns: The melting and casting processes can produce harmful emissions if not managed correctly.
- Material Limitations: Not all metals are suitable for die casting, which can limit options for certain applications.
The Future of Die Casting
The future of die casting looks bright with advancements in technology and growing market demand. Innovations such as:
- 3D Printing: The integration of 3D printing in die making is set to revolutionize the industry by reducing lead times and costs.
- Automation: The use of robotics and automated systems will dramatically improve production efficiency.
- Sustainable Practices: Emphasizing green technologies and materials will align with global sustainability goals.
Conclusion
Die casting is a corner-stone process in the field of metal fabrication, providing significant benefits across various industries. Understanding the intricacies of this process, its applications, and future trends can empower manufacturers to make informed decisions that enhance their operations.
As the industry evolves and incorporates new technologies and practices, die casting will continue to play a pivotal role in shaping the future of manufacturing.
Contact Us
For more information on die casting and how Deep Mould can assist you in your metal fabrication needs, feel free to contact us.