The Essential Guide to Plastic Moulding Parts in Industrial Manufacturing
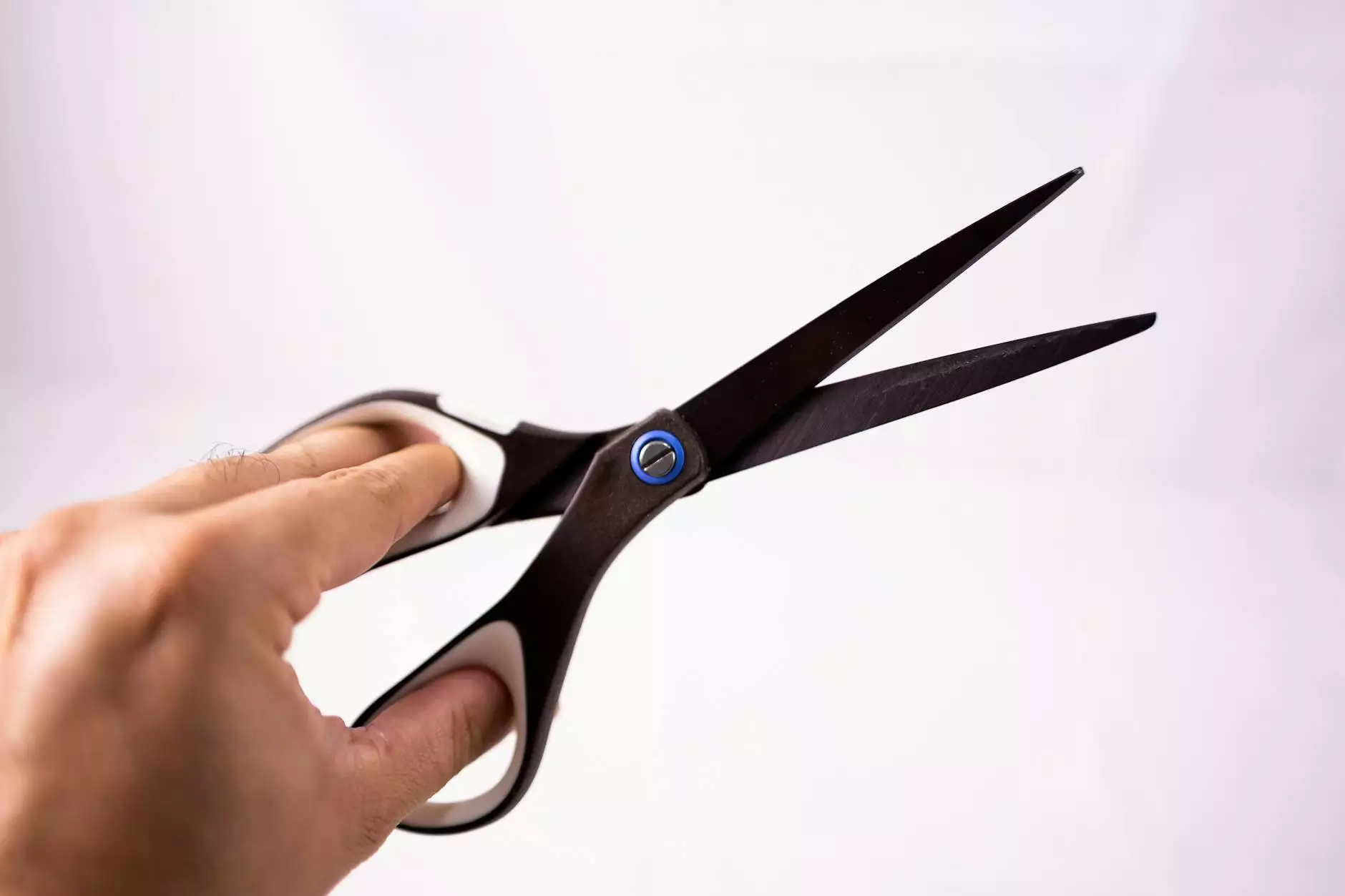
Plastic moulding parts are integral to modern manufacturing, serving as the backbone of countless products across various industries. From consumer goods to industrial machinery, the versatility and durability of these components make them a popular choice among manufacturers. In this comprehensive guide, we will explore the nuances of plastic moulding parts, their applications, and the processes involved in producing them.
Understanding Plastic Moulding Parts
Plastic moulding is a manufacturing process where plastic materials are shaped into desired forms using molds. This technique can produce various parts with intricate designs and specifications. The moulding process is highly efficient, allowing for mass production while maintaining consistent quality. Common types of plastic moulding include:
- Injection Moulding
- Blow Moulding
- Extrusion Moulding
- Compression Moulding
Benefits of Using Plastic Moulding Parts
The use of plastic moulding parts offers numerous advantages that make them a favored choice in the manufacturing sector:
- Cost-Effective: Plastic moulding allows for large production runs, reducing the per-unit cost significantly.
- Lightweight: Plastic parts are lighter than metal alternatives, leading to reduced shipping costs and easier handling.
- Versatile Design: Complex geometries can be achieved, accommodating intricate designs that might be challenging with metals.
- Corrosion Resistance: Plastic materials do not rust or corrode, enhancing the longevity of the parts.
- Color Customization: Plastics can be easily colored and finished, allowing for branding and aesthetic considerations.
Key Applications of Plastic Moulding Parts
Plastic moulding parts are ubiquitous across various sectors, including:
1. Automotive Industry
The automotive sector relies heavily on plastic moulding for components such as:
- Dashboards
- Panels and Trims
- Under-the-hood components
- Light covers and housings
2. Electronics and Appliances
In electronics, plastic moulded parts are used for:
- Casings
- Connectors
- Switch housings
- Insulators
3. Medical Devices
The medical field benefits from plastic moulding due to:
- Lightweight, sterilizable components
- Bio-compatible materials
- Cost-effective production of single-use items
4. Consumer Goods
From toys to household items, consumer goods frequently utilize plastic moulded parts, which gives manufacturers the flexibility needed to innovate and respond to market demands.
Specialized Manufacturing Techniques Related to Plastic Moulding Parts
In addition to traditional plastic moulding, several specialized techniques enhance the capabilities and applications of these parts:
Machining
Machining complements the production of plastic moulding parts by allowing for precise adjustments and modifications. This is essential for parts that require high tolerance levels or unique features that cannot be achieved through moulding alone.
Laser Cutting
Laser cutting is a technology that uses focused laser beams to cut materials with high precision. This technique is often used to create complex shapes from plastic sheets, which can then be further moulded or assembled into finished products.
Welding
Welding techniques have been developed for plastics, allowing manufacturers to join parts together without relying on adhesives. This method can result in stronger, more reliable joints in consumer products and industrial applications.
Plastic Injection Moulding
Plastic injection moulding is the most common method for creating plastic parts. It involves injecting molten plastic into a mold, where it cools and hardens. This process supports rapid production and is perfect for high-volume runs.
Vulcanization
Vulcanized plastics undergo a chemical process that enhances their durability and stability. This is particularly useful in applications requiring high-performance materials, such as automotive and aerospace components.
Choosing the Right Plastic Moulding Supplier
Choosing the right supplier for your plastic moulding parts is crucial for ensuring quality, consistency, and timely delivery. Here are some criteria to consider when selecting a vendor:
- Expertise and Experience: Look for suppliers with a proven track record in the industry, particularly within your specific sector.
- Technology and Equipment: Assess the modernity of their machinery and their capacity to handle complex designs.
- Material Selection: Ensure they offer a variety of materials to suit your needs, including biodegradable and specialized plastics.
- Quality Assurance: Verify that the supplier employs strict quality control measures throughout the production process.
- Customer Service: Evaluate their customer support and how responsive they are to inquiries and issues.
The Future of Plastic Moulding Parts in Industry
The future of plastic moulding parts looks promising as industries continue to innovate and seek sustainable solutions. Trends affecting the future include:
- Eco-Friendly Materials: With an increasing demand for sustainability, manufacturers are developing biodegradable plastics that minimize environmental impact.
- Advanced Manufacturing Techniques: Technologies such as 3D printing are changing the landscape of manufacturing and could supplement traditional moulding methods.
- Customization: The ability to produce bespoke parts on-demand will enhance the efficiency and flexibility of manufacturing processes.
- Integration of Smart Technologies: Incorporating sensors and intelligence into plastic components may lead to the development of 'smart' products.
Conclusion
In conclusion, plastic moulding parts play a critical role in modern manufacturing across multiple industries. Understanding their applications, manufacturing processes, and the evolving technology associated with them is essential for any business looking to stay competitive. By leveraging specialized techniques like machining, laser cutting, welding, and more, manufacturers can create high-quality, durable parts that meet the demands of today’s market.
For those interested in high-quality machined parts, laser cutting, welding, and industrial supplies, consider partnering with reputable suppliers like Sumiparts. Their extensive expertise in manufacturing ensures that your projects will meet the highest standards, driving your business towards success.